Overcoming the Challenges of Oil Analysis in Harsh and Remote Locations
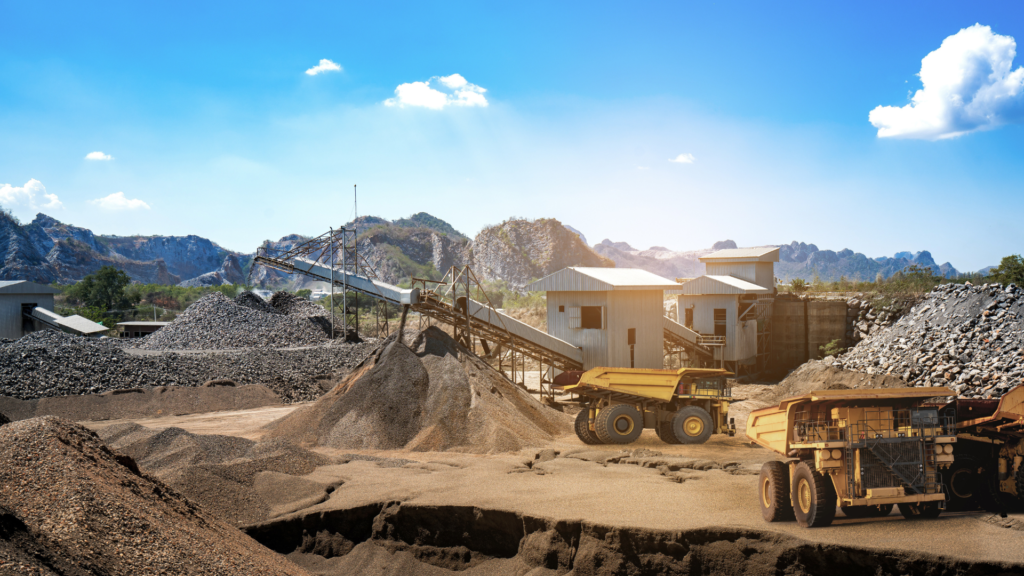
The role of oil analysis is becoming more critical as industrial plants and machinery become more complex with each passing day.
As predictive maintenance programs are important to manage machinery uptime, machine condition monitoring using oil analysis provides early indications of equipment wear and identifies the root causes of corrosion.
Remote Location
Many industrial sites, like mines, that use off-road vehicles are situated at remote locations. It can be difficult for them to rely on outside lab analysis to test the used oil because it can take weeks to send samples into a lab and receive results.
By the time they determine that there is a problem with the vehicle, it has been returned to service and could potentially suffer a major breakdown. Testing oil on-site allows them to make instant service decisions and keep their vehicles running.
Harsh Environments
Construction and mining equipment operate in conditions that are hard on the components. The nature of the work they do exposes the vehicles to large amounts of contamination and debris that can cause damage, especially to the hydraulics and gears which are sensitive to particulate contamination.
Lubricating oil at elevated temperatures can react with oxygen and nitrogen in the atmosphere, as well as sulfur in fuel, to form undesirable by-products that can affect the oil’s viscosity and lead to corrosion or damage to the equipment.
Another element is water contamination. The presence of water can alter the viscosity of a lubricant as well as cause chemical changes resulting in additive depletion and the formation of acids, sludge, and varnish.
Expensive Oil Drains and High Repair Costs
By monitoring oil conditions with on-site analysis, the maintenance staff can determine if the oil drain interval can be extended safely. Reducing the number of oil drains required per vehicle by even just one time per year can provide significant savings across a fleet of vehicles, especially when it involves the large vehicles used in mining and construction.
Oil analysis can help identify potential problems early before they become catastrophic and incur costly repairs. The on-site analysis provides the service technicians the information about the vehicle while it is still in the garage so that repairs can be made immediately before it goes back out on the road.
Large mining and construction equipment can be enormously expensive to repair so catching a small problem before it becomes a major issue can be huge cost savings.
Vehicle Downtime Impacts Service and Revenue
Equipment and vehicles in the construction, mining, and agricultural industries are frequently exposed to severe environmental and harsh working conditions. When a vehicle is unavailable due to mechanical problems, it means it is not available to provide the necessary service.
In the public sector, for example, having a city transit bus or a snow remover unavailable during an emergency will bring chaos to public utilities and cause major concerns to public safety. For companies like freight haulers or mining equipment, it means it will impact the revenue-generating services it provides.
Having an effective oil analysis program will keep important assets in operation by reducing unexpected failures and costly unscheduled downtime. The benefits of an on-site oil analysis maintenance program, like the ones from DKSH and AMETEK Spectro Scientific, include to:
- Deliver rapid results
- Lower operating costs
- Reduce unscheduled downtime
- Increase machine availability
- Extend equipment life
- Decrease total lifecycle equipment costs
- Provide immediate retest capability
Contact us to find out more about the MiniLab 153 oil analysis solutions and how they can help your business save time, reduce costs, and minimize equipment downtime.
Sources: