How 3D Bioprinting Is Advancing the Biomedical Industry
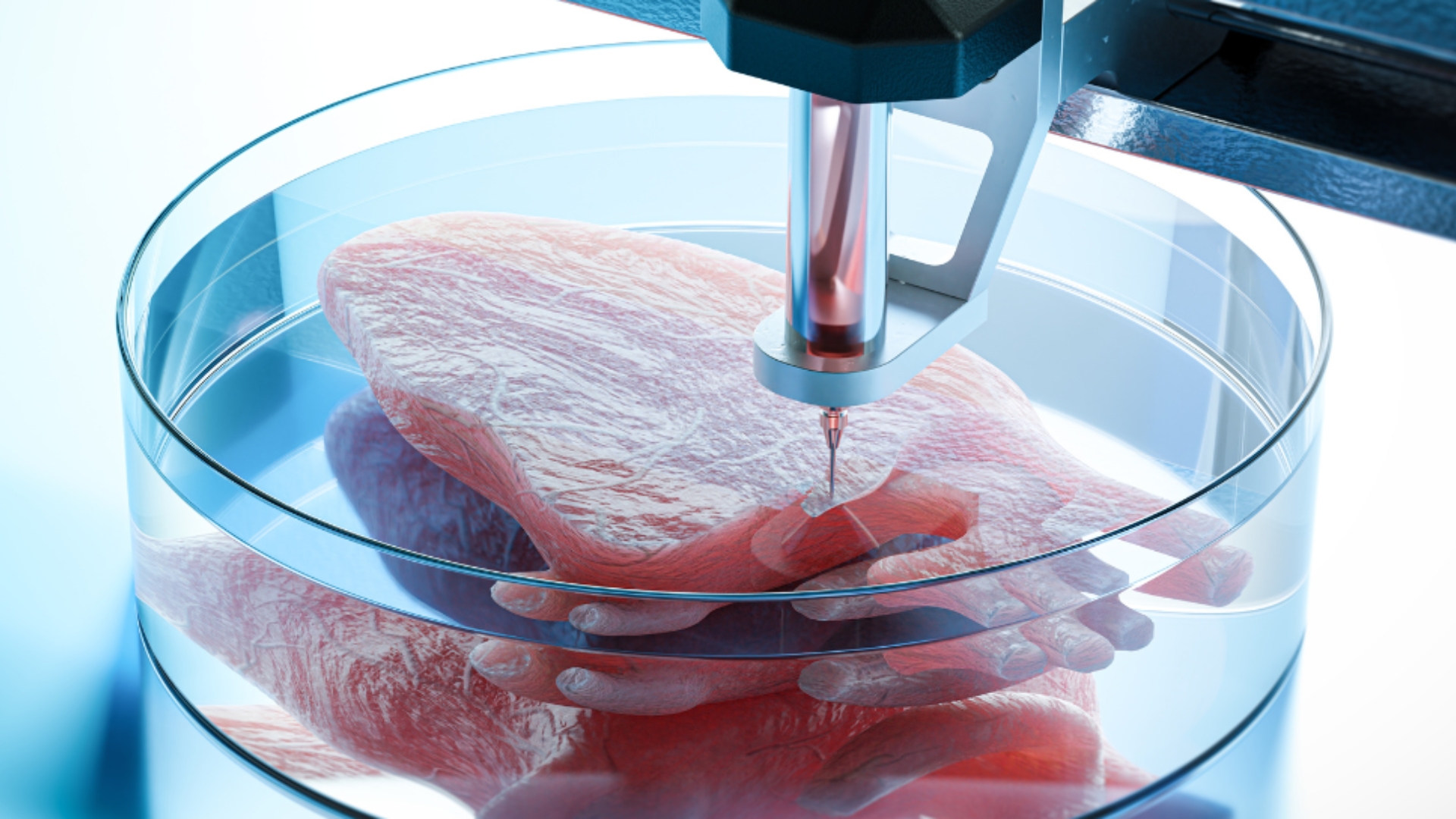
Three-dimensional (3D) bioprinting is an additive manufacturing method that involves printing biomedical structures by deposition of viable cells, biological molecules, and biomaterials in a layer-by-layer fashion to create 3D structures like tissues and organs.
An advanced form of 3D printing using bio-inks made from living cells and biomaterials to create three-dimensional tissue-like structures that can mimic the complexity of human tissues or organs. It is commonly used in regenerative medicine, tissue engineering, and the development of custom prosthetics.
How It Works
The 3D bioprinting process involves several key steps, each crucial to developing viable and functional biological structures. Researchers or scientists begin by extracting and culturing cells from a donor or stem cell. These cells are then combined with hydrogel or another biomaterial that supports cell growth and viability. The process is known as bio-ink formation.
Using a bioprinter, typically through an extrusion or light-based method, layers of bio-inks are deposited according to a digital model. Once the structure is printed, it is incubated to allow the cells to grow and form functional tissues.
Journey to 3D Bioprinting
The journey from 2D to 3D bioprinting represents an evolution of technology that has fundamentally changed how we think about creating tissues and organs for research, medical applications, and beyond.
Before 3D bioprinting emerged, tissue engineering was primarily limited to 2D cell cultures. In this approach, cells were grown on flat surfaces like petri dishes or culture plates. This method was essential for understanding cellular behavior, drug testing, and basic biology, but it had some major limitations.
Poor predictability: Many cells lose their natural characteristics over time in 2D culture, leading to changes in gene expression and function that do not match the vivo conditions.
Flat (monolayer) growth: Cells grow in a monolayer, which does not mimic the 3D environment of real tissues. This affects cell behavior, differentiation, and interactions.
Poor cell-cell and cell-ECM interactions: Real tissues rely on complex interactions between cells and their surrounding ECM. 2D culture fails to replicate this, making it less predictive for tissue-specific studies.
Susceptibility to pharmacological action: 2D cell culture increases the susceptibility to pharmacological action, leading to misleading drug efficacy and toxicity results. This affects drug discovery, testing, and clinical translation in several ways.
Early stages of 3D cell culture development are through the cultivation of a spheroid. A spheroid is a 3D cell culture model that mimics the in vivo microenvironment of tissues and tumors. Spheroids are formed when cells aggregate and grow in a three-dimensional structure, allowing for more physiologically relevant studies compared to traditional 2D cultures.
Among the advantages of a spheroid over 2D cell culture include:
- More physiologically relevant 3D structure
- Improved cell-cell and cell-ECM interactions
- Enhanced cell viability and longevity
- Better drug testing accuracy and disease modeling
The 2010s saw significant advances in bioprinting technology, leading to more sophisticated, high-resolution 3D tissues and organ models. This period marked the development of techniques capable of printing multi-cellular structures with more realistic organization and properties.
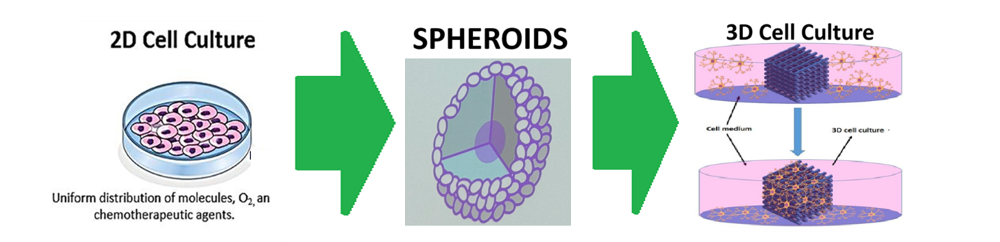
Benefits of 3D Bioprinting
3D bioprinting offers several unique advantages over traditional methods of tissue engineering and medical manufacturing. It represents a significant leap forward in various fields like medicine, pharmaceutical research, tissue regeneration, and personalized healthcare. Here are some of the key advantages of 3D bioprinting.
More predictive data: 3D bioprinting provides highly predictive data by recreating realistic tissue structures, natural cell interactions, and functional vascular networks. This leads to more accurate drug testing, better disease models, and improved personalized medicine.
Lower dependency on animal models: 3D bioprinting reduces the reliance on animal models by creating human-like tissues and organ models, offering more ethical and accurate alternatives for drug testing, disease modeling, and regenerative medicine.
Faster conclusions: 3D bioprinting accelerates drug testing, disease research, and tissue engineering by offering highly controlled, reproducible, and human-relevant models. Unlike traditional methods, 3D bioprinting reduces time-consuming processes like animal trials and manual cell culture experiments, leading to faster and more reliable conclusions.
Long-Term cost saving: 3D bioprinting offers long-term cost savings by reducing reliance on animal models, speeding up the research and development process, and minimizing material wastage and labor costs. These advantages lead to faster time-to-market, more accurate and efficient drug testing, and the personalization of treatments, ultimately providing a significant return on investment in the long run.
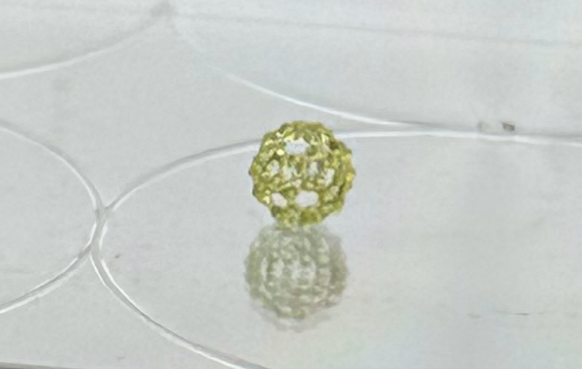
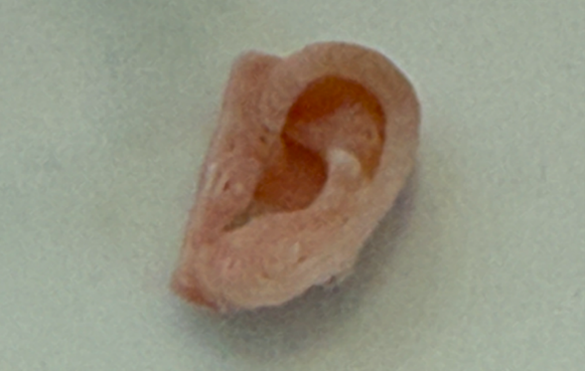
In conclusion, 3D bioprinting is a game-changing technology that holds immense potential in biomedical research, drug development, and personalized medicine. With its ability to create accurate, reproducible, and functional tissue models, it is poised to reduce the reliance on animal testing, accelerate research timelines, and lower costs in the long run.
Reach out to us at DKSH Business Unit Technology for more information on 3D bioprinting.
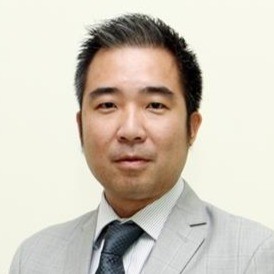
About the Author
Damien Teo is the General Manager, Semiconductor & Electronics and Life Science Solutions at DKSH Business Unit Technology in China. He has over 20 years of experience in the semiconductor and electronics industry, specializing in sales and marketing, product management, and business development. His specialties are in the areas of power management, microcontrollers, and semiconductor solutions. He holds a Master’s in Business Administration from Nanyang Technological University in Singapore and a Diploma in Mechatronics from Singapore Polytechnics.
Damien Teo
Life Science